干式压(ya)缩成型工艺:高纯粉(fen)末(mo)(mo)属(shu)于贫瘠材料,不能用传统工艺成型。首(shou)先,通过添加一定量的(de)表面(mian)活(huo)性(xing)剂,改变(bian)粉(fen)末(mo)(mo)的(de)表面(mian)性(xing)质,包括(kuo)颗(ke)(ke)粒(li)表面(mian)的(de)吸附性(xing)质和粉(fen)末(mo)(mo)颗(ke)(ke)粒(li)的(de)形状,从而降(jiang)低超细粉(fen)末(mo)(mo)的(de)团聚效应(ying),使其均匀分布。增加润滑剂减少颗粒之间及颗粒与模具表面的摩擦;加入黏合剂增强粉料的粘结强度。将粉体进行上述预处理后装入模具,用压机或专用干压成型机以一定压力和压制方式使粉料成为致密坯体。成为可加工陶瓷
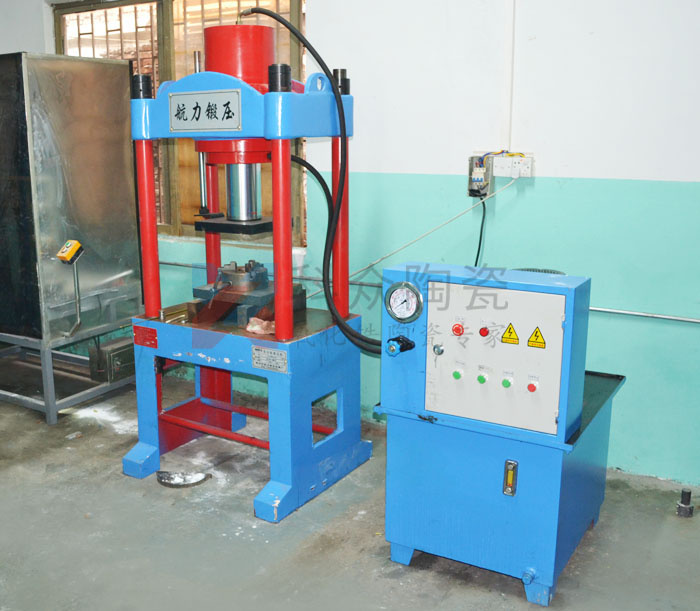
干压成型机
下面就上述几方面因素对干压成型的影响分述如下:
A、模具的光洁度和配合情况:
干压成型对模具质量要求较高,首先要求模具硬度达到一定的要求。由于氧化锆稳定料的颗粒很细,流动性差,因而对模具的光洁度要求很高,若光洁度达不到要求,则干压时影响料的流动,从而导致分层的出现。同时,若模具配合不好,间隙大,则由于氧化锆粉料颗粒细,压制时粉料会从模具间隙中流出,从而造成模具四周的粉料少,这样压制时四周就不能压实,从而会因压力传递不一致而出现分层,故对模具的配合要求较高。
B、成型压力:
成型压力在氧化锆干压成型过程中是较关键的,压力太小和太大都不能压制出理想的坯体。压力太小,则烧后产品的密度小,产品收缩大,坯体压实程度不够容易出现分层;而压力太大,坯体也容易出现裂纹、分层和脱模困难等现象。合适的成型压力需要通过生产实践来摸索。
C、加压方式:
般干压成型时加压方式有两种,一种是单面加压,另一种是双面加压。当单面加压时,则直接受压的一端压力大,出现明显的压力梯度,粉料的流动性越差,则坯体内出现的压力差也就越大,越容易出现分层。双面加压时,坯体两端直接受压,因此两端密度大,中间密度小,其压力梯度的有效传递距离为单面加压的一半,故坯体的密度比单面加压要均匀得多。因此氧化锆陶瓷干压成型时宜采用双面加压的方式。
D、加压速度和保压时间:
加压速度和保压时间控制不好也会造成氧化锆陶瓷坯体出现分层等缺陷。压模下落的速度应缓慢一些,如加压速度过快,则坯体中气体不易排出,从而导致坯体出现分层,表面致密而中间松散,以及存在气泡等现象。如保压时间过短,则压力还未传到应有的深度时,外力就已卸掉,这样坯体中气体不易排出,就难以得到较为理想的坯体,会导致坯体出现分层以及存在气泡等现象。同时保压时间应均匀一致,否则会引起产品厚薄不均,造成废品。
E、脱模方式和脱模速度:
干压脱模时一般采用工具将坯体从模腔中顶出,脱模速度要均匀缓慢,如不注意会引起坯体开裂。实践表明脱模时脱模工具要平整,否则会引起坯体受力不均而造成开裂。总之,干压成型和上述几方面因素都有关系,要成型出理想的坯体,以上各方面都要控制好。
地址://sflude.com/bangzhu/1451.html
本文“工业陶瓷干压成型时应注意什么?”由科众陶瓷编辑整理,修订时间:2020-05-05 17:02:37
科众陶瓷是专业的工业陶瓷加工生产厂家,可来图来样按需定制,陶瓷加工保证质量、交期准时!
有(you)疑问请点击(ji)咨询客服(fu)
- 上一页:什么是氮化铝陶瓷片?
- 下一页:氧化锆陶瓷管与氧化铝陶瓷管具有哪些优势?